Elevate Your Craft: Specialist Insights into Casting Aluminum
Elevate Your Craft: Specialist Insights into Casting Aluminum
Blog Article
Light Weight Aluminum Spreading Providers Introduced: Vital Insights and Tips
Exploring the world of aluminum spreading solutions can introduce a globe of complex processes and nuanced factors to consider that are essential for successful end results. As sectors increasingly turn to light weight aluminum for its lightweight yet durable residential or commercial properties, comprehending the fundamentals of casting ends up being critical. From the essential strategies to the intricate information that can make or damage a casting project, there is a wealth of insights and suggestions waiting to be uncovered. So, as we venture into the world of light weight aluminum spreading solutions, prepare to reveal the vital components that can shape the trajectory of your projects and elevate your understanding of this intricate craft.
The Fundamentals of Aluminum Spreading
What essential procedures are included in light weight aluminum casting that form the foundation of this commonly utilized production technique? Light weight aluminum casting is a versatile and cost-efficient technique utilized in various markets to produce facility and detailed steel parts. The process begins with the melting of aluminum ingots in a heating system, generally at temperatures varying from 1220 ° F to 1670 ° F, relying on the specific aluminum alloy being utilized. As soon as molten, the aluminum is poured into a pre-designed mold and mildew tooth cavity, where it strengthens and takes the shape of the mold.
Key factors such as mold and mildew layout, gating system, and cooling down rate play a crucial duty in determining the final quality of the cast aluminum part. The mold can be made of numerous materials like investment, steel, or sand spreading wax, relying on the ins and out of the component and the desired surface finish. After solidification, the mold is removed, and the casting undertakes ending up processes such as warmth machining, surface, and treatment finishing to satisfy the called for specifications. Understanding these essential processes is vital for attaining top notch light weight aluminum spreadings with mechanical residential properties and specific dimensions.
Different Casting Techniques Described
Discovering the numerous methods employed in aluminum casting offers valuable insights right into the varied approaches used to accomplish precise and complex steel components. One common technique is sand casting, where a mold and mildew is created making use of compressed sand around a pattern of the wanted component. This strategy is flexible and cost-effective, suitable for both simple and intricate shapes. One more method, pass away spreading, includes injecting liquified aluminum right into a steel mold and mildew under high pressure. Die casting enables high accuracy and repeatability, making it suitable for automation of small to medium-sized components. For even more complex styles, financial investment casting is usually liked. This approach uses wax patterns that are disappeared, leaving a dental caries for the liquified light weight aluminum to fill up. Financial investment spreading returns accurate information and smooth surfaces, making it popular in markets such as aerospace and auto. Each spreading technique has its one-of-a-kind advantages and is chosen based on factors such as complexity, volume, and expense considerations.
Aspects to Consider When Picking a Provider
When selecting a light weight aluminum casting solution company, evaluating their experience and expertise is important for making sure top quality and reliability in the manufacturing process. The copyright's experience in the field suggests their experience with different casting techniques, possible difficulties, and finest methods. It is necessary to ask about the kinds of tasks they have serviced in the past, guaranteeing they align with the complexity and specs of your own project.
Additionally, consider the provider's reputation within the sector. Seek testimonials, endorsements, and case researches that demonstrate their capacity to provide premium aluminum castings constantly. A trustworthy service provider will commonly have qualifications or associations with industry organizations, showcasing their dedication to quality and adherence to sector requirements.
In addition, assess the copyright's abilities in terms of personalization, quantity demands, and task timelines. Make sure that they can suit your details demands and have the versatility to range production as required. Effective interaction and transparency concerning expenses, preparation, and quality assurance processes are additionally essential aspects to take into consideration when selecting an aluminum casting provider.

Common Challenges and Solutions
Navigating with the intricacies of aluminum casting processes usually offers makers with a series of difficulties that need ingenious options to ensure effectiveness and high quality in manufacturing. One common obstacle encountered in aluminum casting is the formation of issues such as porosity, shrinking, or inclusions due to inappropriate mold style or insufficient steel high quality.
Executing sophisticated technologies like computer-aided style (CAD) and computer numerical control (CNC) machining can enhance precision and consistency in aluminum casting. By spending in automation and real-time read monitoring systems, makers can boost procedure control and reduce variants, ultimately enhancing the overall high quality of aluminum cast items.
Tips for Optimizing Your Casting Projects
By making certain that the gating system is well-designed and properly placed, you can enhance the flow of molten light weight aluminum and decrease the chances of flaws in the last casting. Furthermore, using computer system simulations can help in anticipating and assessing the circulation of metal throughout the casting process, allowing for adjustments to be made prior to real manufacturing begins.
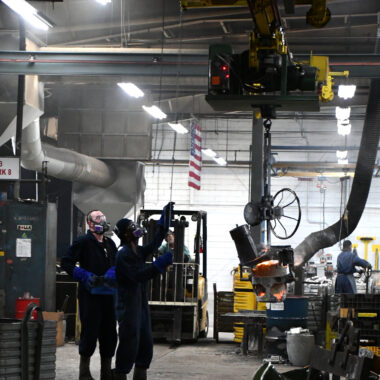
Verdict
Finally, recognizing the fundamentals of light weight aluminum casting, various casting approaches, elements to take into consideration when picking a company, usual obstacles and options, and suggestions for maximizing spreading projects are important Your Domain Name for successful end results. By adhering to these insights and applying finest people, methods and companies can make certain effective and effective light weight aluminum spreading services that fulfill their specific demands and demands.
Understanding these essential procedures is crucial for achieving top notch aluminum spreadings with accurate measurements and mechanical residential or commercial properties.
When selecting a light weight aluminum casting service copyright, evaluating their experience and proficiency is important for making sure high quality and integrity in the production procedure. Reliable interaction and transparency regarding costs, lead times, and top quality control procedures are additionally essential elements to consider when picking an aluminum casting service provider.
Browsing via the complexities of light weight aluminum casting procedures usually provides manufacturers with a collection of difficulties that need ingenious solutions to make certain effectiveness and her latest blog top quality in manufacturing. One typical challenge dealt with in aluminum spreading is the formation of issues such as porosity, contraction, or incorporations due to inappropriate mold design or insufficient steel top quality.
Report this page